CVP Everest
A perfect box every 3 seconds.
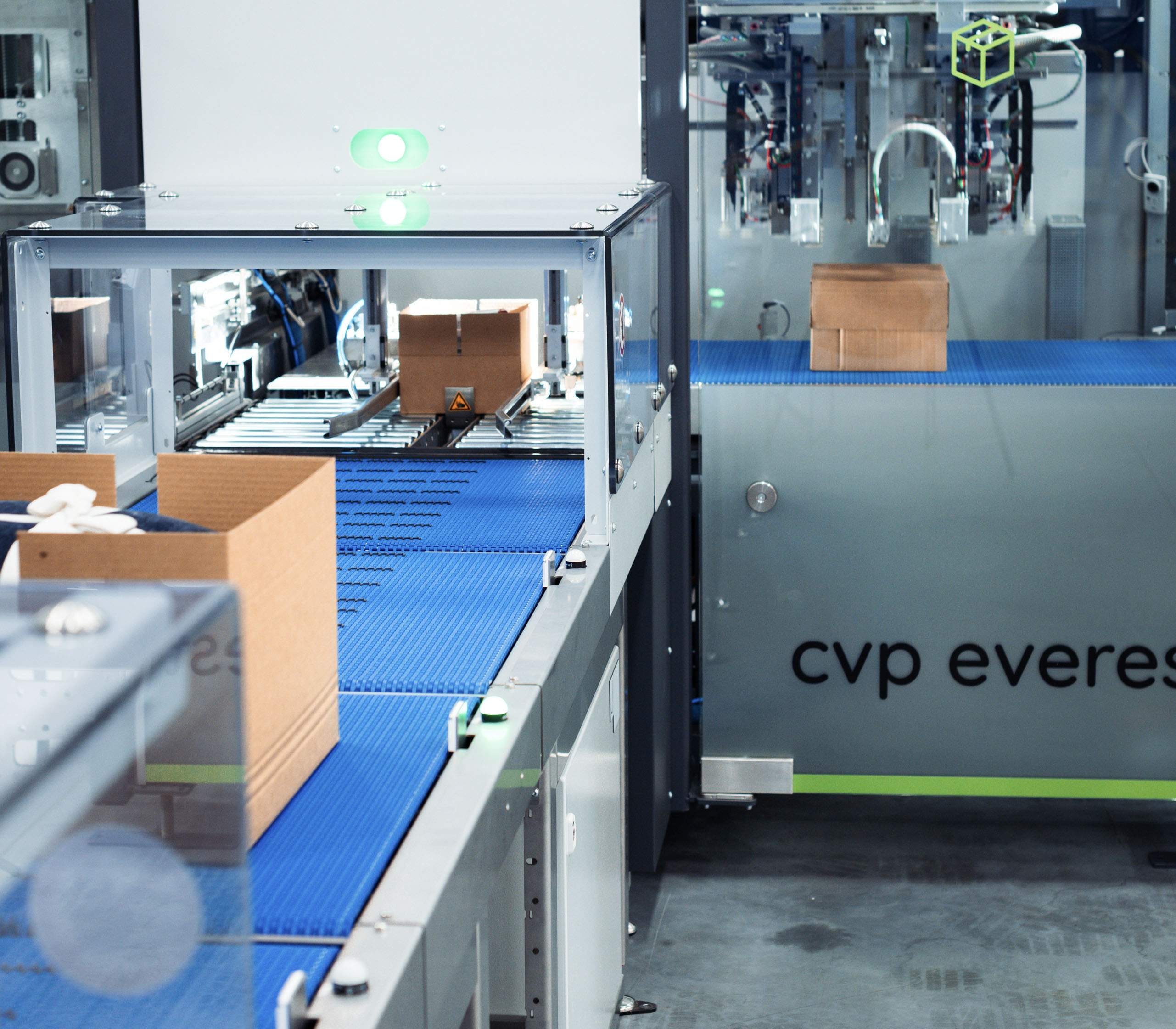
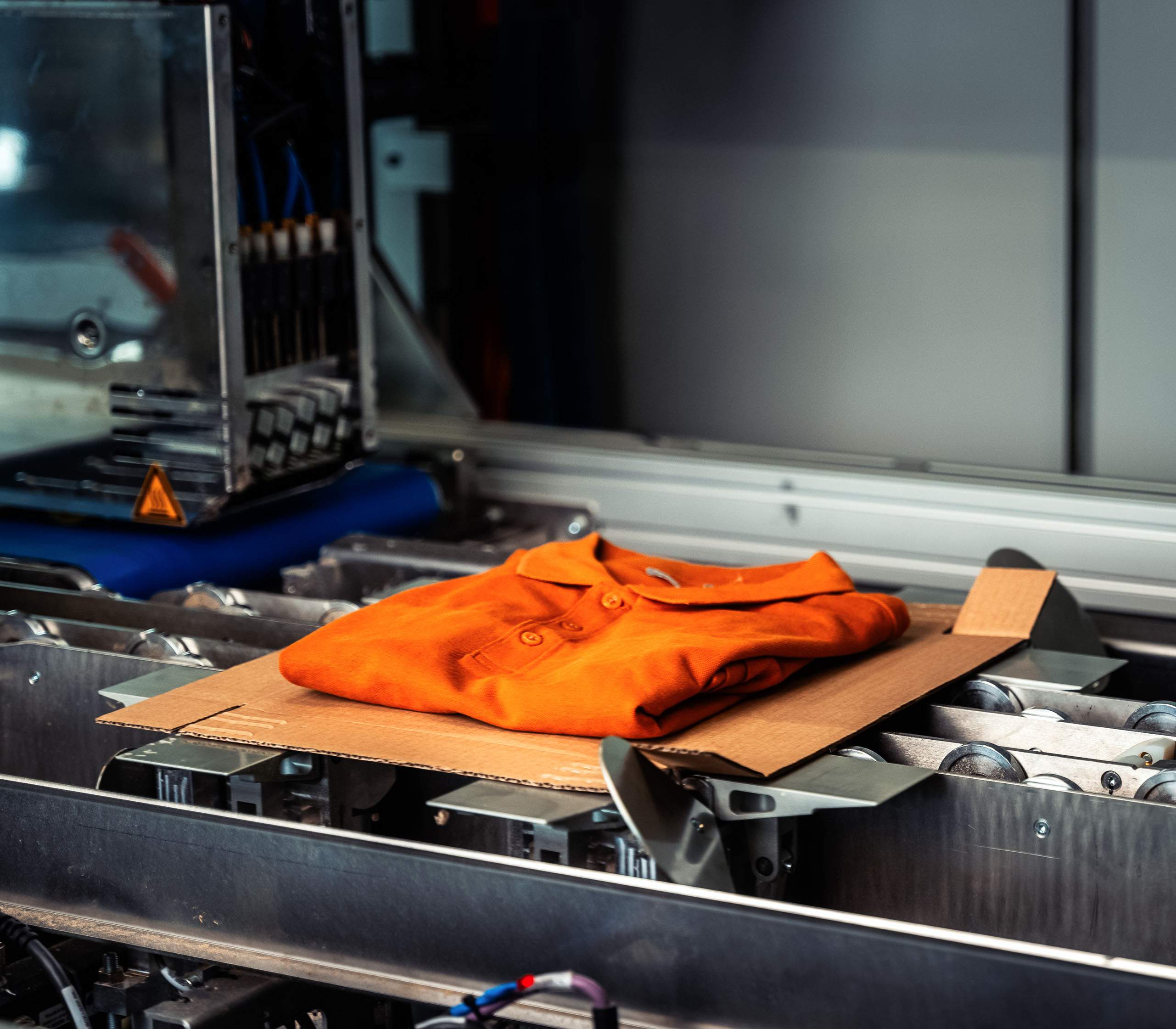
Features & Specs
CVP Everest
Our CVP Everest stands out as the ultimate automated packaging machine, modernizing your fulfillment chain. Experience less stress, lower costs, and reduced waste while gaining more control, capacity, and speed. It’s the ultimate efficiency booster.
-
One, two or three corrugate feeders
» One, two or three corrugate continuous feeders use fan-fold material for dynamic switching and replenishment, reduced inventory, and usage savings.
» Allows for millions of unique box size combinations. We are agnostic to corrugate providers.
» Every CVP machine supports up to 3 uniquely branded corrugate designs.
-
Induct station
» Single or dual induct station supports high operator and machine productivity levels.
» Operator/s scans unique order barcode and places on the input conveyor.
-
Auto infeed
» A universal automated connection between the upstream warehouse and the CVP. Single item orders are automatically inducted into the CVP.
» Optimizes CVP throughput
» Eliminates labor dependence
» No human errors.
-
Base creator
» Our scanner captures 3D images of each unique parcel to determine the minimum box size required.
» Corrugate is cut and creased to form the box and erected around the parcel. Box base is secured with hotmelt and travels via conveyor to the lid creator.
» On demand construction allows for a fit-to-size box in a wide range of sizes with no WMS data needed.
-
Pick to box / Box first
» Create an empty tray using our base creator.
» Use the base to collect orders.
» Close base with lid.
-
Lid creator
» Two lid applicators work in parallel to fully seal each custom box with hotmelt on all four sides.
» Corrugate is cut and creased to form the minimum lid size required to fit the box base, creating a strong, fully closed box.
-
Tear strips
» Optional easy-tear strip/s for customers to open the package.
-
Weighing station
» Order weight verification optimizes rate shopping via an in-line scale, assuring accurate weight and measurements of each parcel.
-
Label print & apply
» Carrier compliant labels are created and applied to ensure accurate delivery.
-
Additional print & apply
» The additional print and apply system enables the addition of one extra label to any parcel.
» Can apply labels for internal logistics processes or for compliance with local and/or global legislation.
-
Custom box printing
» Create a unique experience by adding customer names, package details, or your branding.
» Customize using ink jet printing after the box is created with seasonal, promotional, special offers or other messaging.
-
One, two or three corrugate feeders
» One, two or three corrugate continuous feeders use fan-fold material for dynamic switching and replenishment, reduced inventory, and usage savings.
» Allows for millions of unique box size combinations. We are agnostic to corrugate providers.
» Every CVP machine supports up to 3 uniquely branded corrugate designs.
-
Induct station
» Single or dual induct station supports high operator and machine productivity levels.
» Operator/s scans unique order barcode and places on the input conveyor.
-
Auto infeed
» A universal automated connection between the upstream warehouse and the CVP. Single item orders are automatically inducted into the CVP.
» Optimizes CVP throughput
» Eliminates labor dependence
» No human errors.
-
Base creator
» Our scanner captures 3D images of each unique parcel to determine the minimum box size required.
» Corrugate is cut and creased to form the box and erected around the parcel. Box base is secured with hotmelt and travels via conveyor to the lid creator.
» On demand construction allows for a fit-to-size box in a wide range of sizes with no WMS data needed.
-
Pick to box / Box first
» Create an empty tray using our base creator.
» Use the base to collect orders.
» Close base with lid.
-
Lid creator
» Two lid applicators work in parallel to fully seal each custom box with hotmelt on all four sides.
» Corrugate is cut and creased to form the minimum lid size required to fit the box base, creating a strong, fully closed box.
-
Tear strips
» Optional easy-tear strip/s for customers to open the package.
-
Weighing station
» Order weight verification optimizes rate shopping via an in-line scale, assuring accurate weight and measurements of each parcel.
-
Label print & apply
» Carrier compliant labels are created and applied to ensure accurate delivery.
-
Additional print & apply
» The additional print and apply system enables the addition of one extra label to any parcel.
» Can apply labels for internal logistics processes or for compliance with local and/or global legislation.
-
Custom box printing
» Create a unique experience by adding customer names, package details, or your branding.
» Customize using ink jet printing after the box is created with seasonal, promotional, special offers or other messaging.
Features
-
Machine dimensions
United States:
Length – 102.7 ft
Width – 40.7 ftHeight:
Machine – 10.8 ft
Corrugate feeder – 12.2 ftEurope:
Length – 31,3 meter
Width – 12,4 meterHeight:
Machine – 3,3 meter
Corrugate feeder – 3,7 meter -
Machine weight
United States:
26,455 lbsEurope:
12.000 kilos
-
Box specifications
Imperial:
Minimum:
7.09 x 9.45 x 1.1 inchMaximum:
24.21 x 20.87 x 13.78 inch
24.21 x 24.21 x 10.67 inchMetric:
Minimum:
180 x 240 x 28 mmMaximum:
615 x 535 x 350 mm
615 x 615 x 275 mm -
Machine throughput
» CVP Everest has a machine rate of 1,100 boxes per hour.
-
Corrugate types and branding
United States:
Type – Endless fanfold ~ 1200 ft per pallet
Flute – Single wall B and single wall C
Thickness – 1/8 inch – 1/6 inch
Sizes – 23.6 inch, 31.5 inch, 39.4 inch
ECT – 32 – 44Europe:
Type – Endless fanfold ~ 700 meters per pallet
Flute – Single wall B and single wall C
Thickness – 3.0mm – 4.0 mm
Sizes – 600mm, 800mm, 1000mm
ECT – 32 – 44 -
Monitoring and reporting
» Real-time monitoring and daily performance reporting available in off-the-shelf configurable options.
-
Machine dimensions
United States:
Length – 102.7 ft
Width – 40.7 ftHeight:
Machine – 10.8 ft
Corrugate feeder – 12.2 ftEurope:
Length – 31,3 meter
Width – 12,4 meterHeight:
Machine – 3,3 meter
Corrugate feeder – 3,7 meter -
Machine weight
United States:
26,455 lbsEurope:
12.000 kilos
-
Box specifications
Imperial:
Minimum:
7.09 x 9.45 x 1.1 inchMaximum:
24.21 x 20.87 x 13.78 inch
24.21 x 24.21 x 10.67 inchMetric:
Minimum:
180 x 240 x 28 mmMaximum:
615 x 535 x 350 mm
615 x 615 x 275 mm -
Machine throughput
» CVP Everest has a machine rate of 1,100 boxes per hour.
-
Corrugate types and branding
United States:
Type – Endless fanfold ~ 1200 ft per pallet
Flute – Single wall B and single wall C
Thickness – 1/8 inch – 1/6 inch
Sizes – 23.6 inch, 31.5 inch, 39.4 inch
ECT – 32 – 44Europe:
Type – Endless fanfold ~ 700 meters per pallet
Flute – Single wall B and single wall C
Thickness – 3.0mm – 4.0 mm
Sizes – 600mm, 800mm, 1000mm
ECT – 32 – 44 -
Monitoring and reporting
» Real-time monitoring and daily performance reporting available in off-the-shelf configurable options.
Tech specs
Strength in numbers
50%
in volume savings
30%
in material savings
20
manual packing stations
What makes Sparck spark?
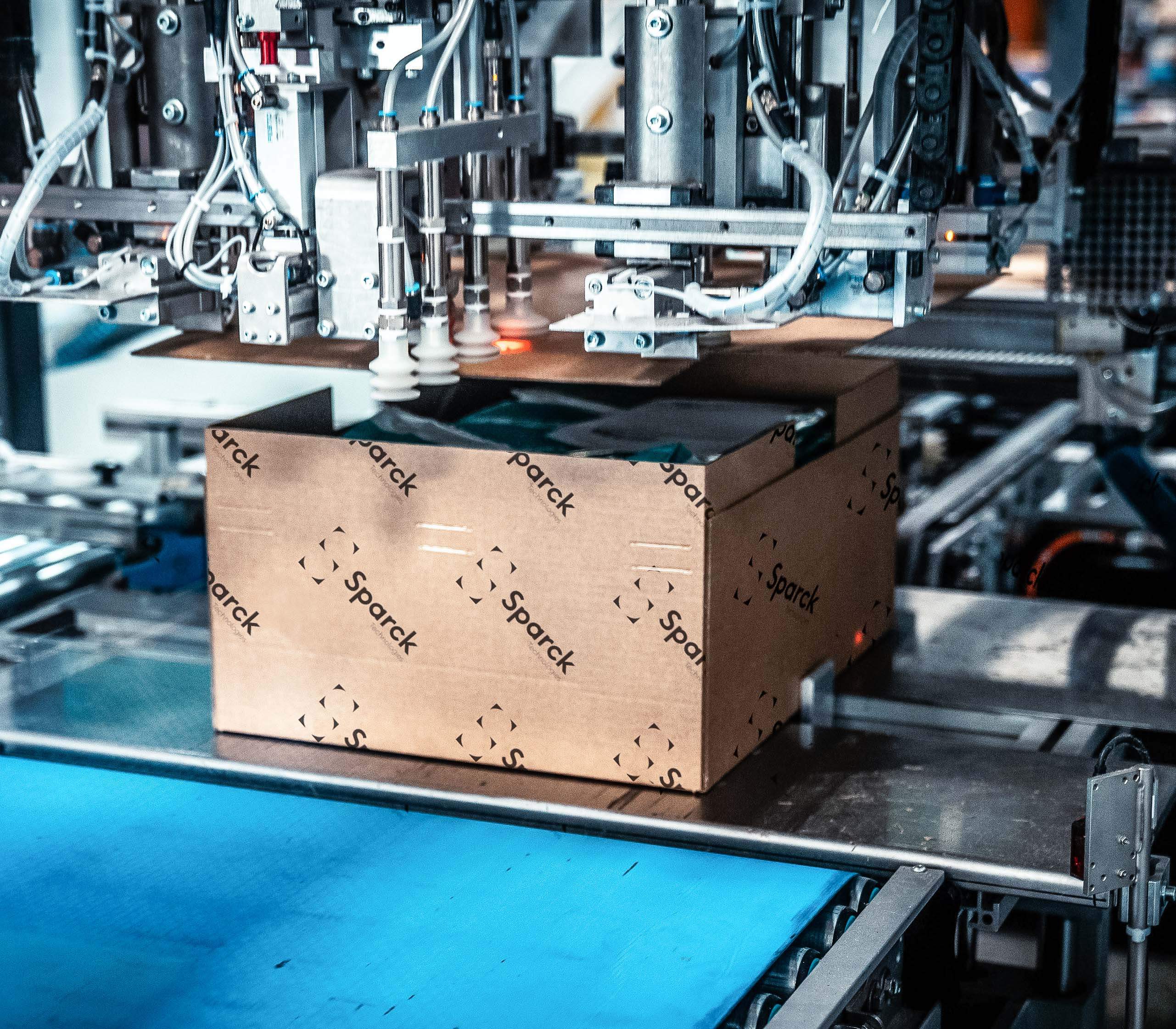
The best service in the industry
Our dedicated support team is committed to ensure your success every step of the way.
- Remote support
- Sparck training
- Support from Sparck's own experts
- Installation time: two weeks
- User friendly interface and handling
- Error handling - fastest in the business
- 24/7 in-house expert advice
How to buy
Time to upgrade your packaging game? Get in touch with our sales team, download our buyers guide or crunch those numbers with our sustainability calculator.